
Página focada em metodologias e aplicação da mentalidade enxuta e redução de desperdícios.
Mostrando postagens com marcador Custos industriais. Mostrar todas as postagens
Mostrando postagens com marcador Custos industriais. Mostrar todas as postagens
sábado, 17 de fevereiro de 2018
Como completar um FMEA
Neste artigo, iremos discutir o FMEA ou Análise de Modos de Falha e Efeitos
Cada produto ou processo está sujeito a diferentes tipos ou modos de falha e as possíveis falhas todos têm consequências ou efeitos.
O FMEA é usado para:
- Identificar as potenciais falhas e os riscos relativos associados projetados em um produto ou processo.
- Priorizar planos de ação para reduzir esses potenciais falhas com maior risco relativo.
- Acompanhar e avaliar os resultados dos planos de ação.
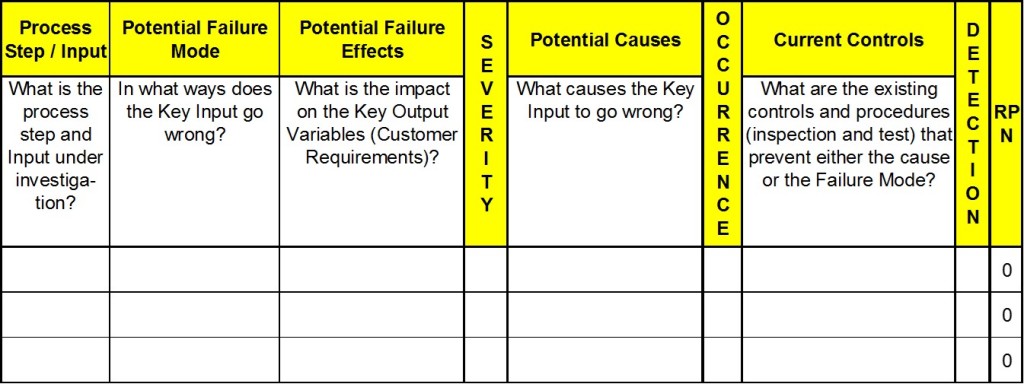
Os passos para completar um FMEA:
Comente e rotular as etapas do processo (usando o seu mapa de processo) e a função pretendida ou funções desses passos.
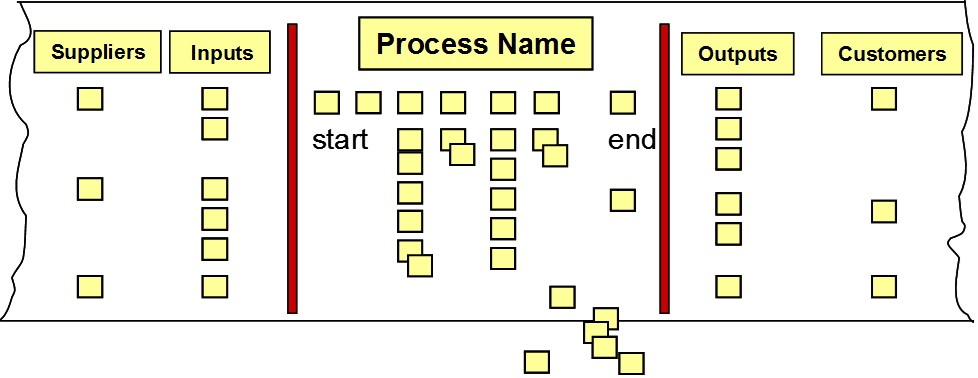
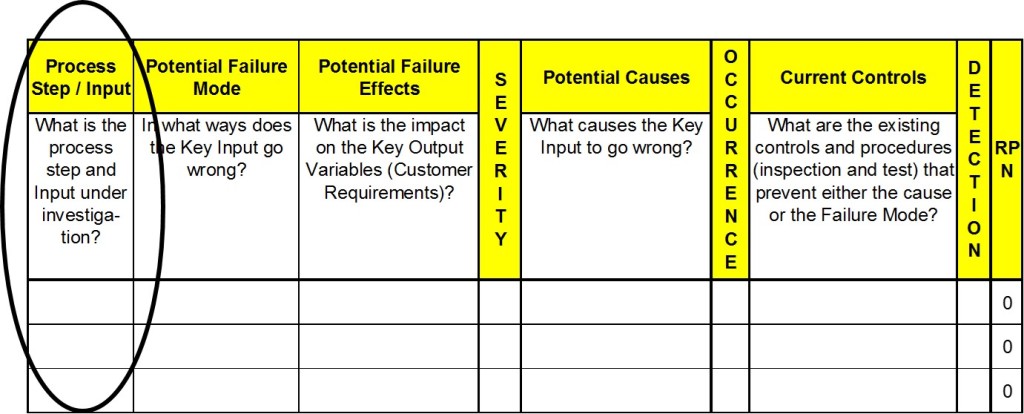
2. Considere os possíveis modos de falha para cada componente e sua função correspondente.
Um modo de falha potencial representa qualquer forma em que o passo componente ou processo poderia deixar de exercer a sua função ou funções pretendidas.
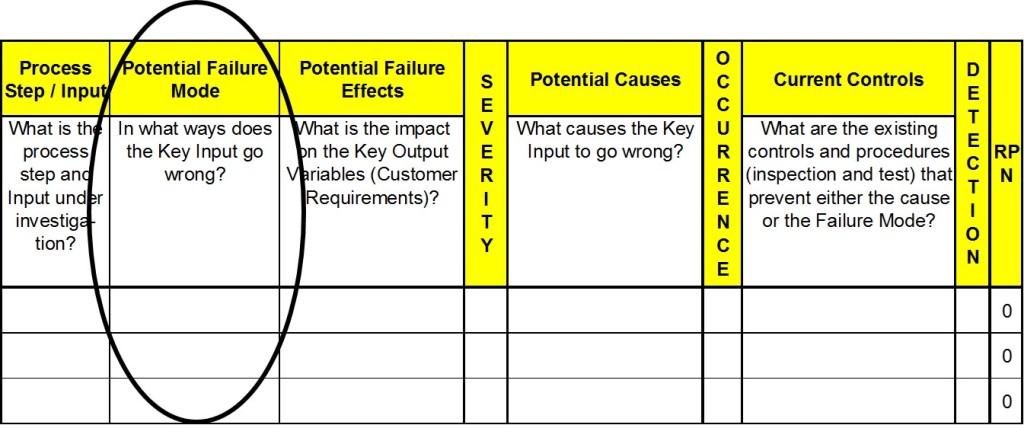
3. Determinar os efeitos potenciais falhas associadas a cada modo de falha. O efeito está relacionado directamente com a capacidade de esse componente específico para realizar a sua função pretendida.
O efeito deve ser expressa em termos significativos para o desempenho do produto ou sistema.
Se os efeitos são definidas em termos gerais, será difícil identificar (e reduzir) os verdadeiros riscos potenciais.
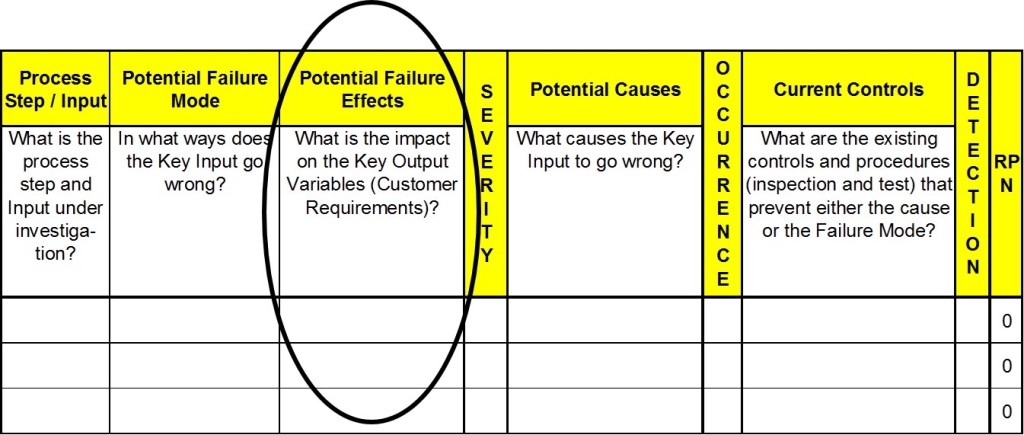
4. Para cada modo de falha, determinar todas as causas de raiz potencial.
Use ferramentas classificadas como ferramenta Root Cause Analysis, bem como o melhor conhecimento e experiência da equipe.
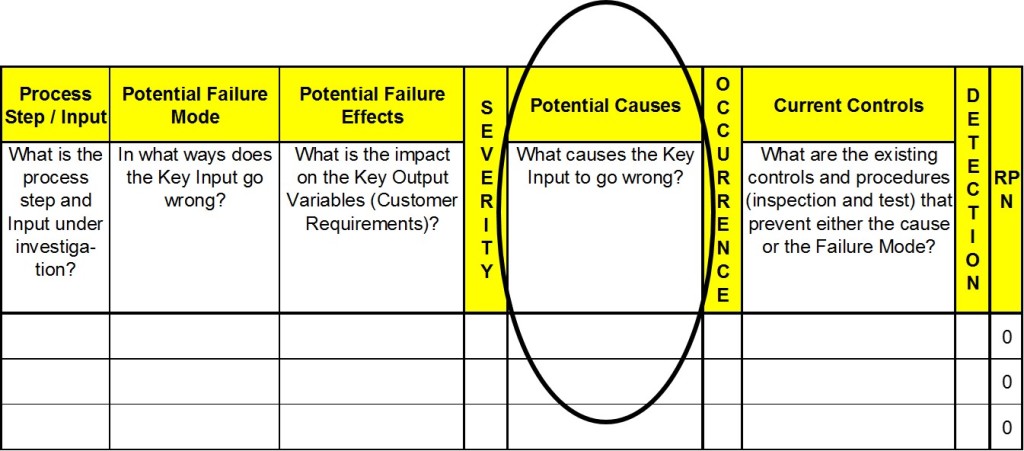
5. Para cada causa, identificar Controls processo atual. Estes são testes, procedimentos ou mecanismos que você tem agora no lugar para manter falhas de chegar ao cliente.
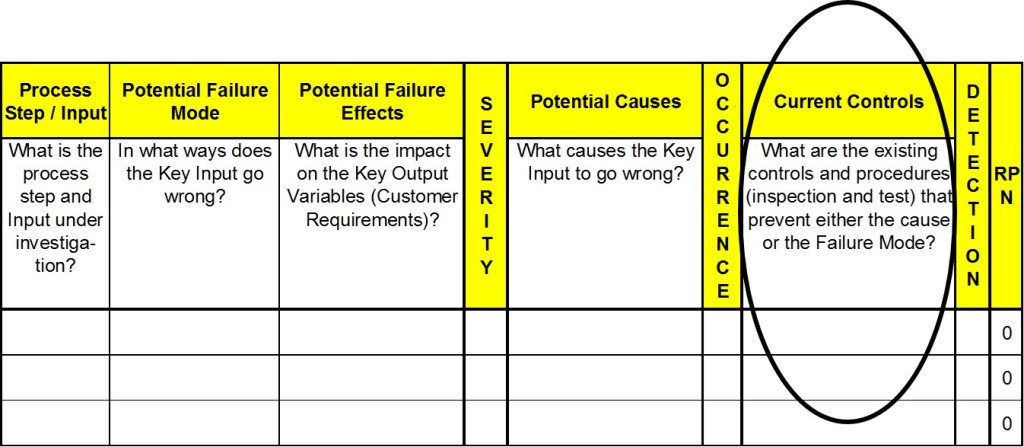
6. Atribuir uma gravidade de classificação para cada efeito que foi identificado.
O Ranking Gravidade é uma estimativa de quão sério um efeito seria caso ocorra.
Para determinar a gravidade, considere o impacto do efeito teria sobre o cliente, sobre as operações a jusante, ou sobre os funcionários que operam o processo.
O Ranking Gravidade baseia-se numa escala relativa variando de 1 a 10.
A “10” significa que o efeito tem uma gravidade perigosamente alto levando a um perigo sem aviso.
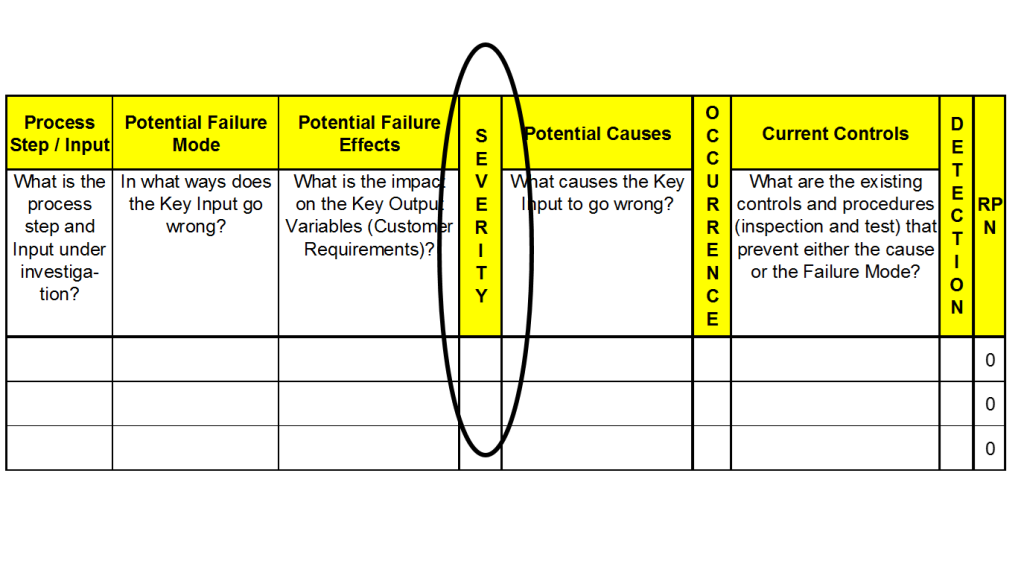
Amostra de uma escala de gravidade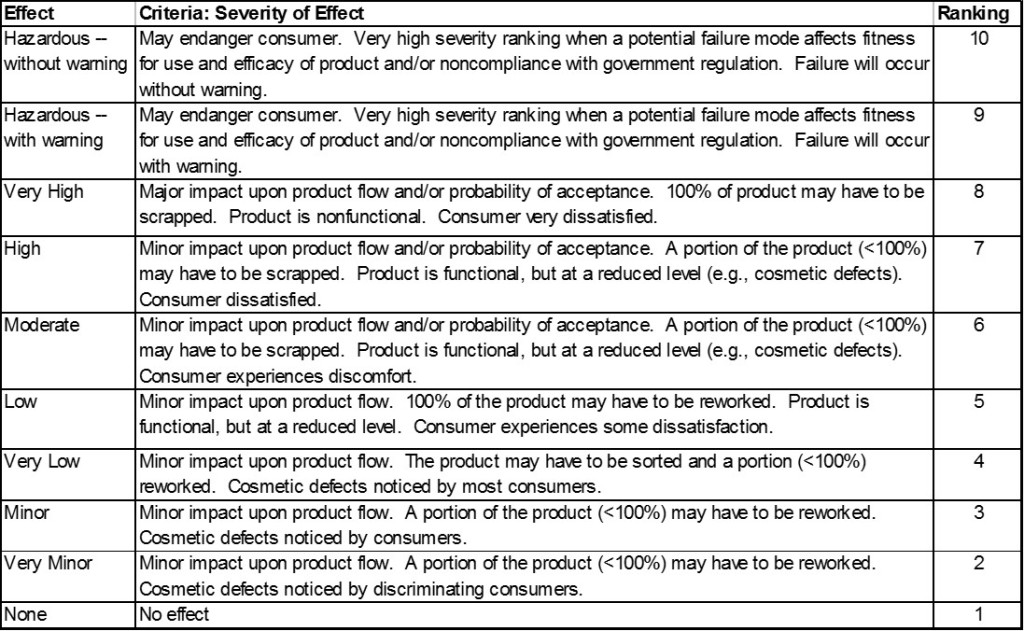
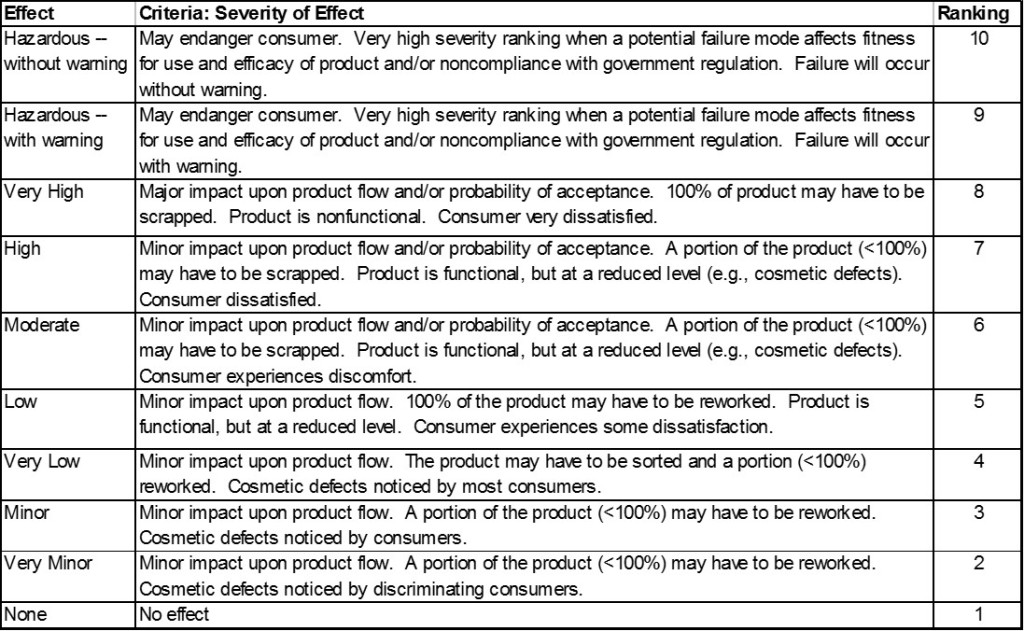
7. Atribuir a Ocorrência Ranking
O Ranking Ocorrência baseia-se na probabilidade, ou frequência, que a causa (ou mecanismo de falha) vai ocorrer.
Uma vez que a causa é conhecida, capturar dados sobre a freqüência de causas. Fontes de dados pode ser sucata e retrabalho relatórios, reclamações de clientes e registros de manutenção de equipamentos. 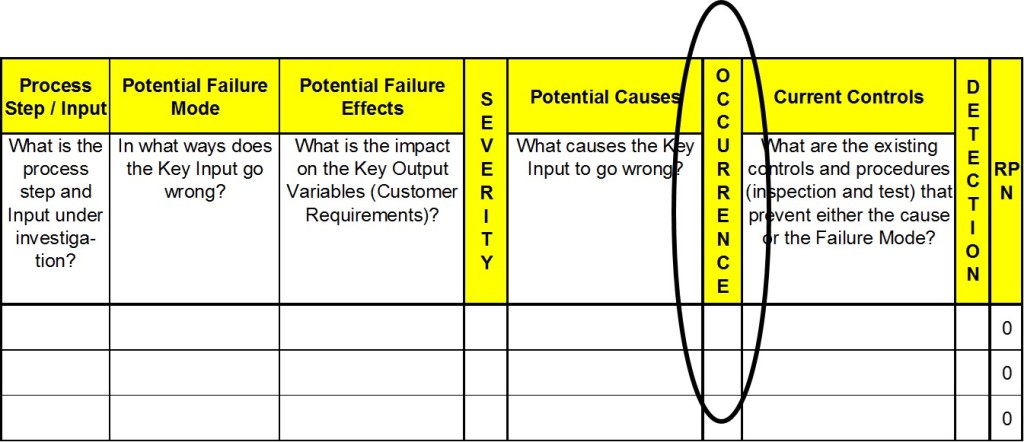
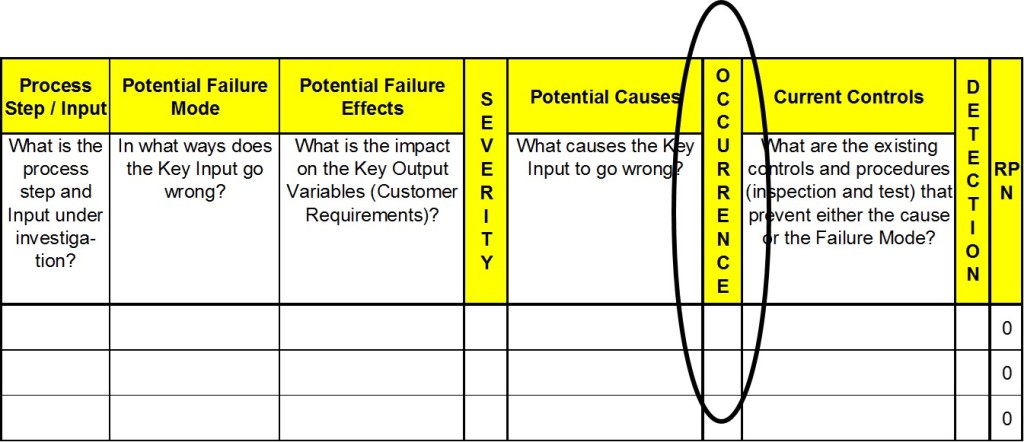
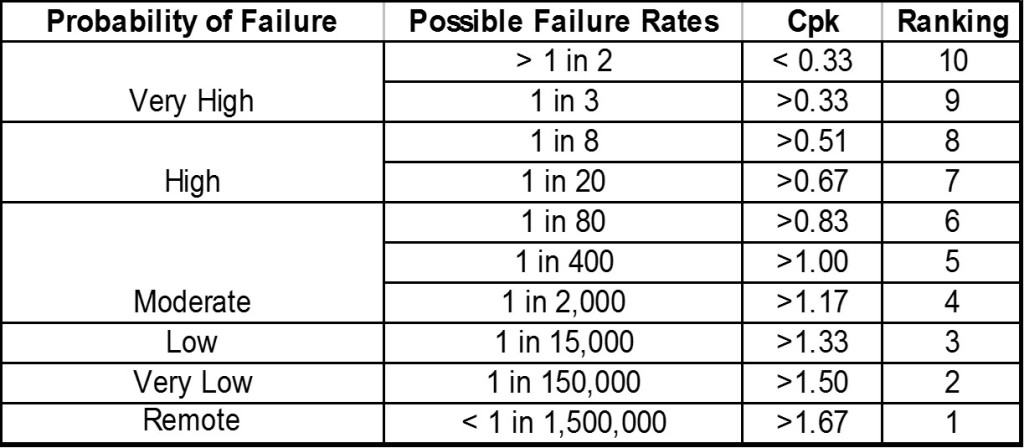
8. Atribuir o classificações Detecção
Para atribuir a classificação de detecção, identificar o processo ou controlos relacionados com o produto no lugar para cada um dos modos de falha e depois atribuir uma classificação de detecção para cada controlo. rankings de detecção de avaliar os controles de processos actualmente em vigor.
Um controlo pode relacionar-se a si mesmo de modo de falha, a causa (ou mecanismo) de falha, ou os efeitos de um modo de falha.
Para tornar os controlos avaliaram ainda mais complexo, os controlos podem impedir um modo de falha ou causa a ocorrência ou detectar um modo de falha, causa da falha, ou efeito de falha após ter ocorrido.

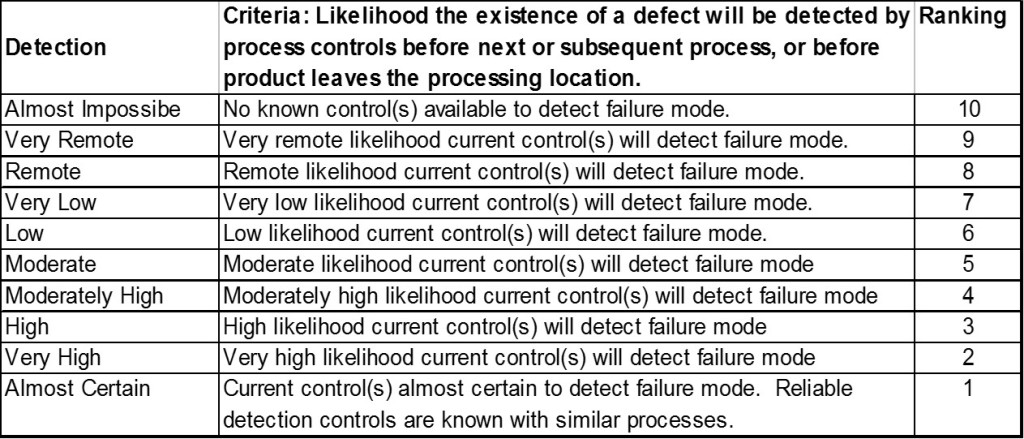
9. Calcular o Número de Prioridade de Risco (RPN)
A RPN é o Número de Prioridade de Risco. A RPN nos dá uma classificação de risco relativo. Quanto maior o RPN, maior o risco potencial.
A RPN é calculado multiplicando-se as três classificações juntos. Multiplique o ranking Times Gravidade da Ocorrência ranking do Times ranking de Detecção.
Calcular a RPN para cada modo de falha e efeito.
Priorizar os riscos, classificando o RPN de maior pontuação para baixo Score. Isto irá ajudar a equipe a determinar os inputs mais críticos e as causas de seu fracasso.
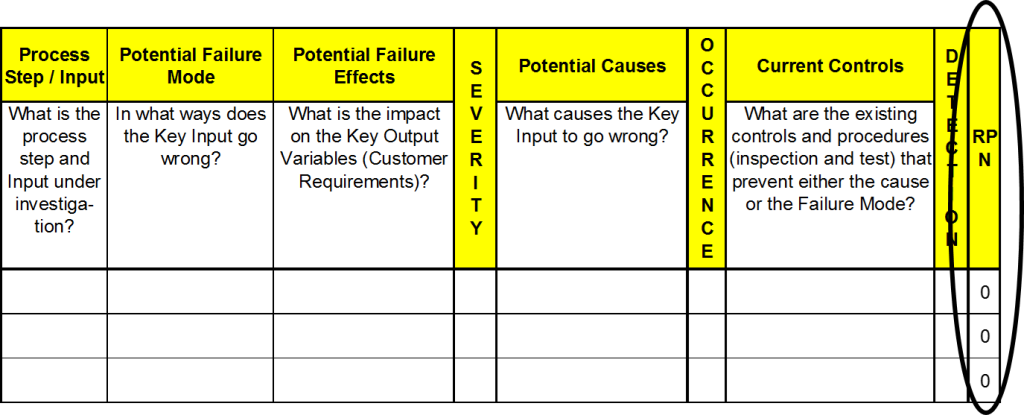
10. Desenvolver Plano de Acção:
Tomando acção significa reduzir a RPN. A RPN pode ser reduzida baixando qualquer das três classificações (gravidade, ocorrência, ou detecção) individualmente ou em combinação um com o outro.
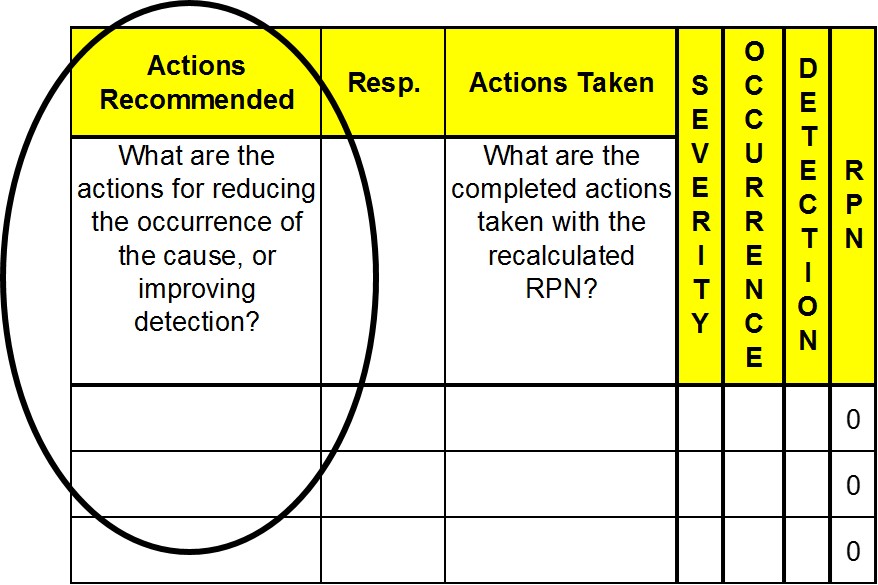
11. Quem é responsável:
Este é um passo muito importante na tomada de medidas!
Certifique-se de incluir pessoa (s) responsável e do prazo
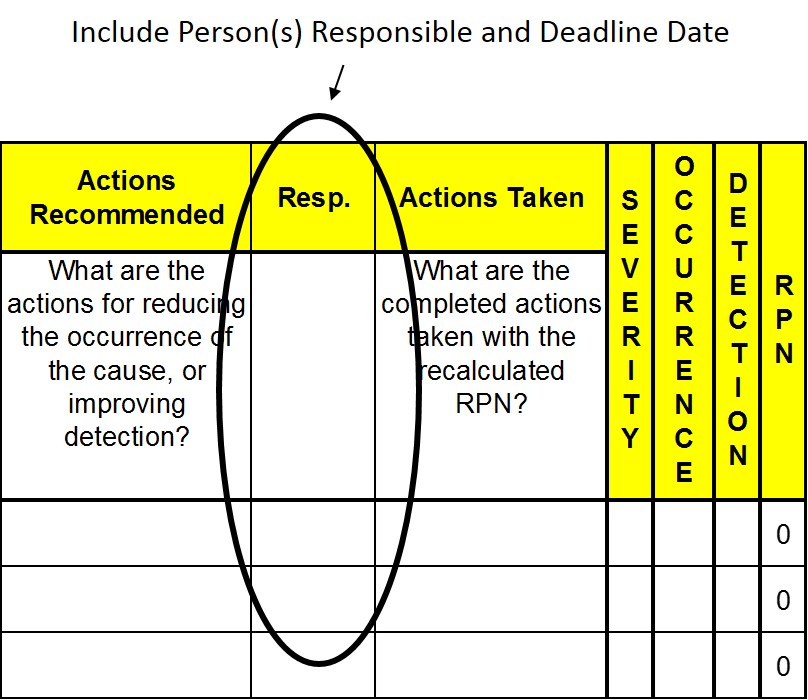
12. agir:
O plano descreve quais os passos necessários para implementar a solução, que vai fazê-las, e quando eles vão ser concluída.
A maioria dos planos de acção identificados durante um PFMEA será do simples “quem, o quê, e quando” categoria.
Responsabilidades e datas de conclusão alvo para ações específicas a serem tomadas são identificados.
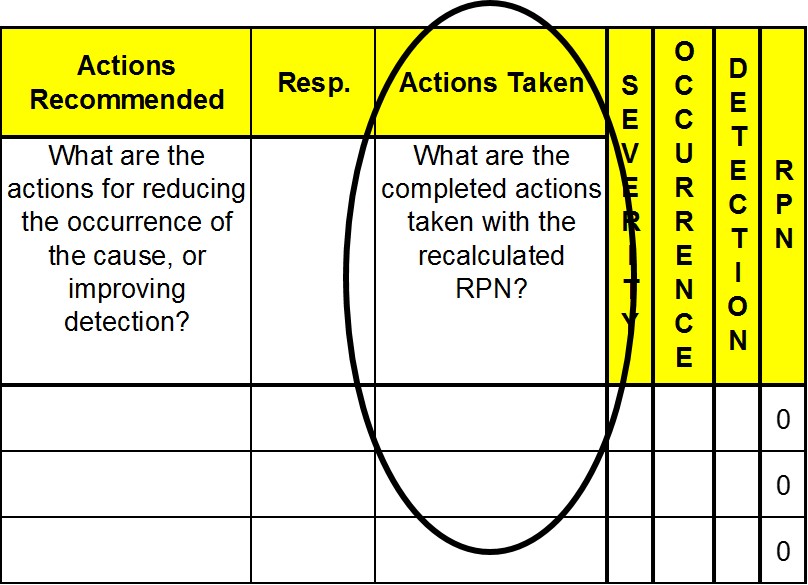
13. recalcular o RPN Resultante:
Este passo de um PFMEA confirma o plano de acção teve os resultados desejados, calculando a RPN resultante. Para recalcular a RPN, reavaliar a gravidade, a ocorrência e rankings de detecção para os modos de falha após o plano de acção foi concluída.
sábado, 23 de setembro de 2017
Métodos de custeio de produção de forma prática - Parte 1
Um dos pontos mais complexos no ambiente industrial é apurar de forma assertiva os custos reais dos produtos produzidos, para essa tarefa árdua existe algumas metodologias que possibilitam padronizar a apuracão e termos melhor exatidão na definição dos custos reais de produção.
Os pontos que iremos abordar será uma decomposição das 3 metodologias mais usadas na formação de custo, bem como a forma de sua aplicação, passando por todos os pontos que o compõe e suas formas de cálculo, o intuito é que no final dos 4 artigos dessa série, tenhamos clareza de como efetivamente os custos de produção são montados e como relacionamos esses custos com os objetivos gerais da empresa.
A primeira parte na formação de custo está relacionada ao conhecimento do produto, como ele é composto e qual o processo produtivo que existe para que ele seja produzido, para exemplificar as explicações usaremos um produção padrão, abaixo as características desse produto:
Nome do Produto: Caixa de presente.
Tamanho: 12 Cm de altura X 15 Cm de comprimento X 12 Cm de largura.
Consumo de Matéria Prima: 1,25 metros de papel.
Custo do Metro de Papel: 2 reais
Descrição do processo de fabricação: O nosso processo de fabricação está dimensionado em células de produção, onde cada célula tem uma capacidade de 50 caixas por dia, e está estruturada da seguinte forma:
- Operação de pigmentação do papel, com 2 operadores.
- O processo de corte com 1 operador.
- E no final o processo de montagem e acabamento com 2 operadores por células.
O custo por mês de cada operador é de 2.500 reais;
Além dos custos listados anteriormente, ainda existe os chamados custos fixos, que são todos que não estão relacionadas ao volume que será produzido, como as despesas com o prédio da fábrica, os salários dos gerentes, água, energia e etc...
Custo fixos totais por mês de 80.000 reais.
Para o nosso exemplo, iremos produzir uma demanda de 8.000 unidades no mês.
Como nosso exemplo existe apenas 1 tipo de produto, não teremos complicações em montar o custo do produto, conforme abaixo:
Custo de MOD
Demanda mês: 8.000
Dias úteis no mês: 20 dias
Demanda média dia = Demanda mês/Dias úteis = 8000/20 = 400
Capacidade por célula: 50 unidades/dia
Células necessárias = Demanda dia/Capacidade dia = 400/50 = 8
Operadores por células: 5
Total de Operadores = Células necessárias * Operadores por células = 8*5 = 40
Custo por operador: 2.500 reais
Custo total de MOD(Mão de obra direta) = 2500*40 = 100.000 reais
Custo de Matéria prima
Demanda mês: 8.000
Consumo de MP por unidade: 1,25 metro
Custo do metro: 2 reais
Matéria prima necessária total: Consumo por unidade * Demanda total * Custo por metro = 8000 * 1,25 * 2 = 20000
Custo de MP total = 20.000 reais
Custo total = Custo de MOD + Custo de MP + Custos fixos
Custo total = 100.000 + 20.000 + 80.000 = 200.000 reais
Custo por unidade produzida = custo total / total produzido = 200.000 / 8.000 = 25 reais
Apesar do racional para calculo do custo de produção ser simples, é uma ferramenta poderosa quando queremos identificar as alavancas que temos para atuar nos desvios que impactam os custos de produção, e claro que o exemplo que usamos temos apenas um tipo de produto, um único SKU, o que torna nossa análise simples e objetiva. Nos próximos artigos irei mostrar exemplos das metodologias que temos para separar os custos dentro do ambiente produtivo quando tiver produtos diferentes em seus processo, com capacidades produtivas diferentes e linhas de produção diferentes.
Até a próxima.
Assinar:
Postagens (Atom)