Neste artigo, iremos discutir o FMEA ou Análise de Modos de Falha e Efeitos
Cada produto ou processo está sujeito a diferentes tipos ou modos de falha e as possíveis falhas todos têm consequências ou efeitos.
O FMEA é usado para:
- Identificar as potenciais falhas e os riscos relativos associados projetados em um produto ou processo.
- Priorizar planos de ação para reduzir esses potenciais falhas com maior risco relativo.
- Acompanhar e avaliar os resultados dos planos de ação.
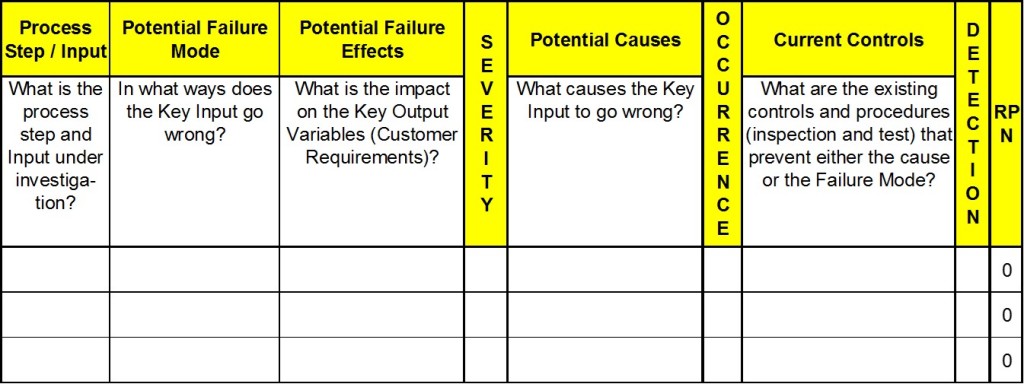
Os passos para completar um FMEA:
Comente e rotular as etapas do processo (usando o seu mapa de processo) e a função pretendida ou funções desses passos.
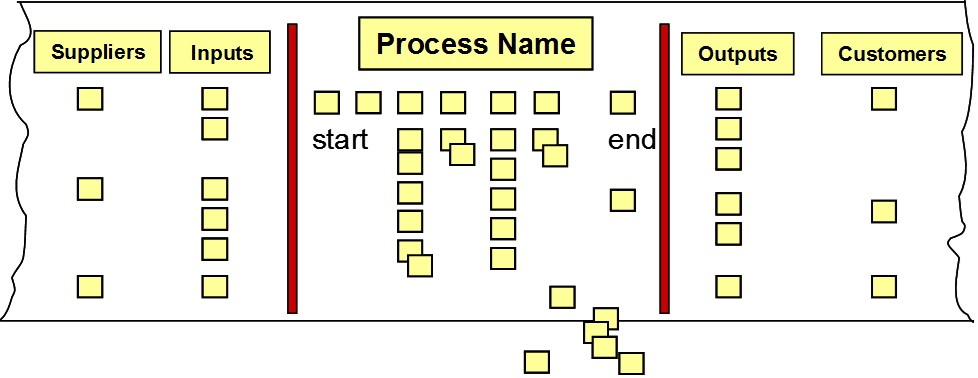
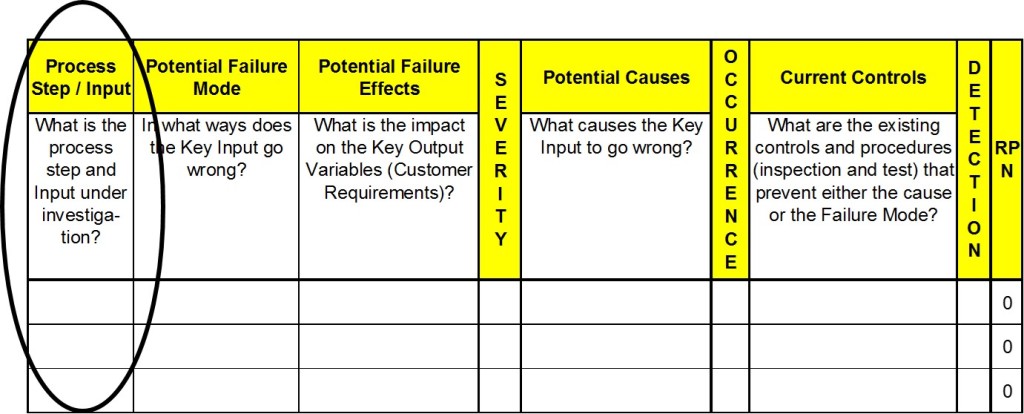
2. Considere os possíveis modos de falha para cada componente e sua função correspondente.
Um modo de falha potencial representa qualquer forma em que o passo componente ou processo poderia deixar de exercer a sua função ou funções pretendidas.
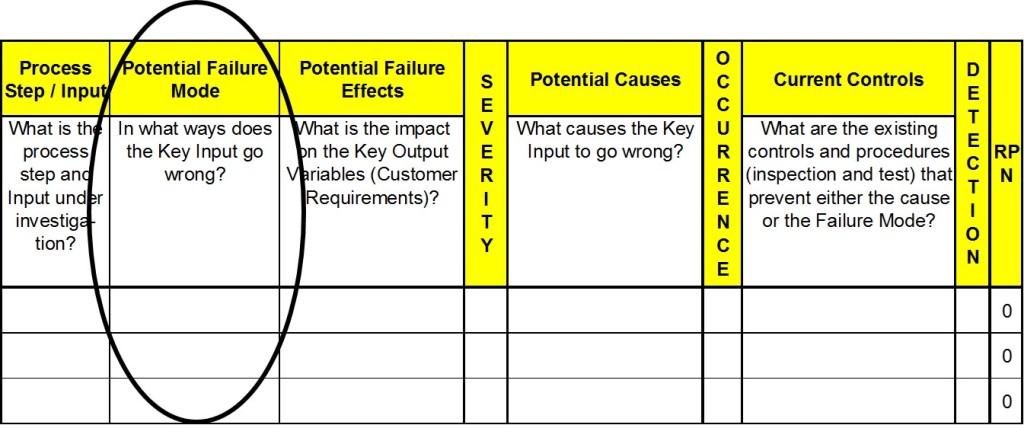
3. Determinar os efeitos potenciais falhas associadas a cada modo de falha. O efeito está relacionado directamente com a capacidade de esse componente específico para realizar a sua função pretendida.
O efeito deve ser expressa em termos significativos para o desempenho do produto ou sistema.
Se os efeitos são definidas em termos gerais, será difícil identificar (e reduzir) os verdadeiros riscos potenciais.
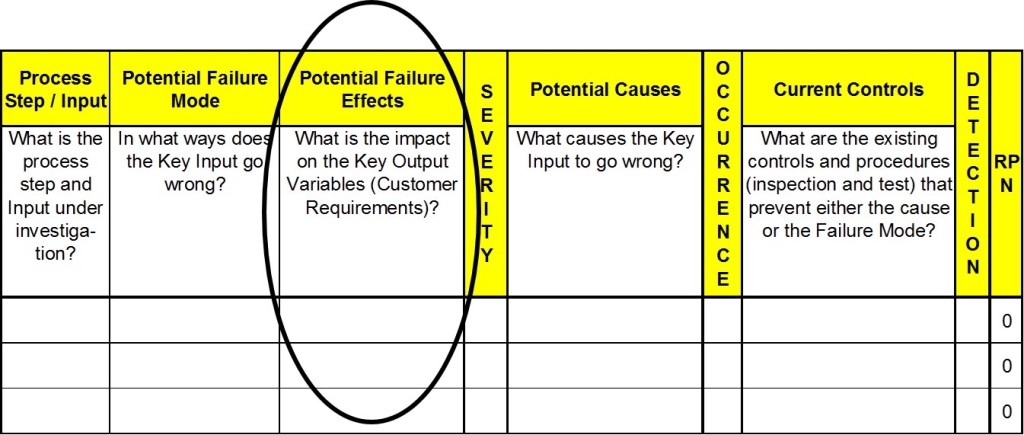
4. Para cada modo de falha, determinar todas as causas de raiz potencial.
Use ferramentas classificadas como ferramenta Root Cause Analysis, bem como o melhor conhecimento e experiência da equipe.
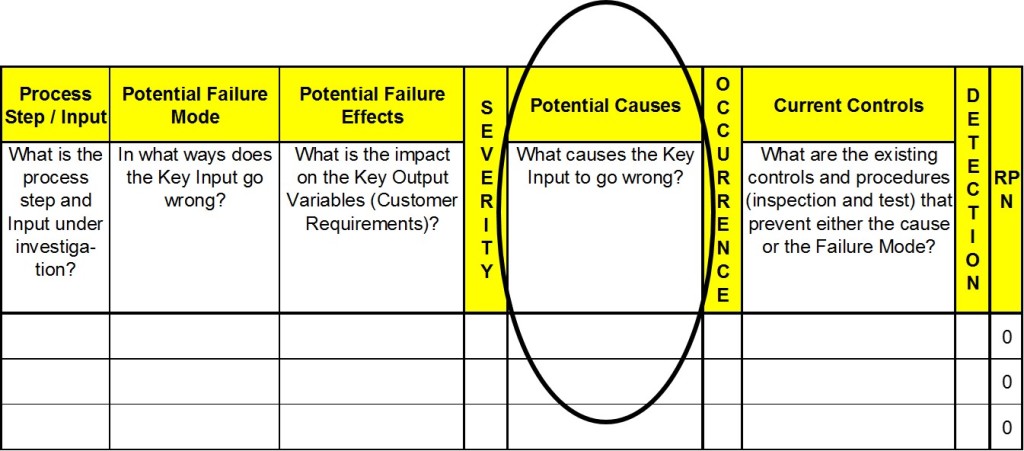
5. Para cada causa, identificar Controls processo atual. Estes são testes, procedimentos ou mecanismos que você tem agora no lugar para manter falhas de chegar ao cliente.
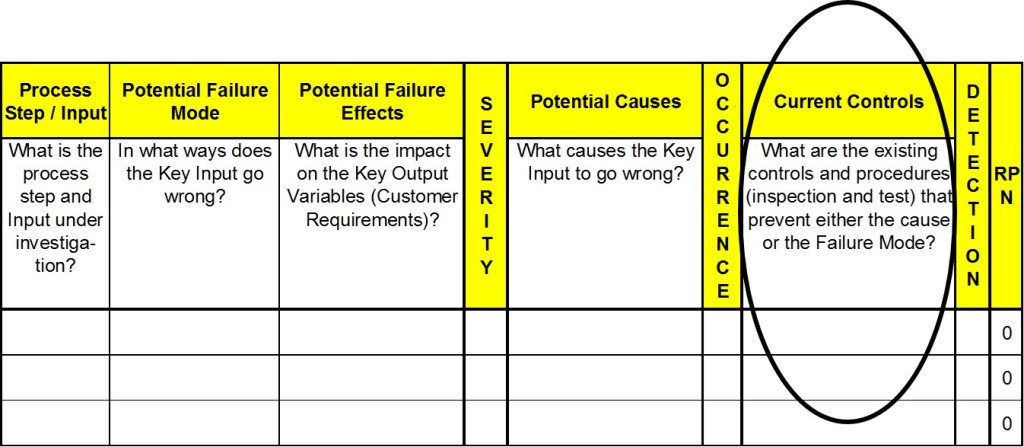
6. Atribuir uma gravidade de classificação para cada efeito que foi identificado.
O Ranking Gravidade é uma estimativa de quão sério um efeito seria caso ocorra.
Para determinar a gravidade, considere o impacto do efeito teria sobre o cliente, sobre as operações a jusante, ou sobre os funcionários que operam o processo.
O Ranking Gravidade baseia-se numa escala relativa variando de 1 a 10.
A “10” significa que o efeito tem uma gravidade perigosamente alto levando a um perigo sem aviso.
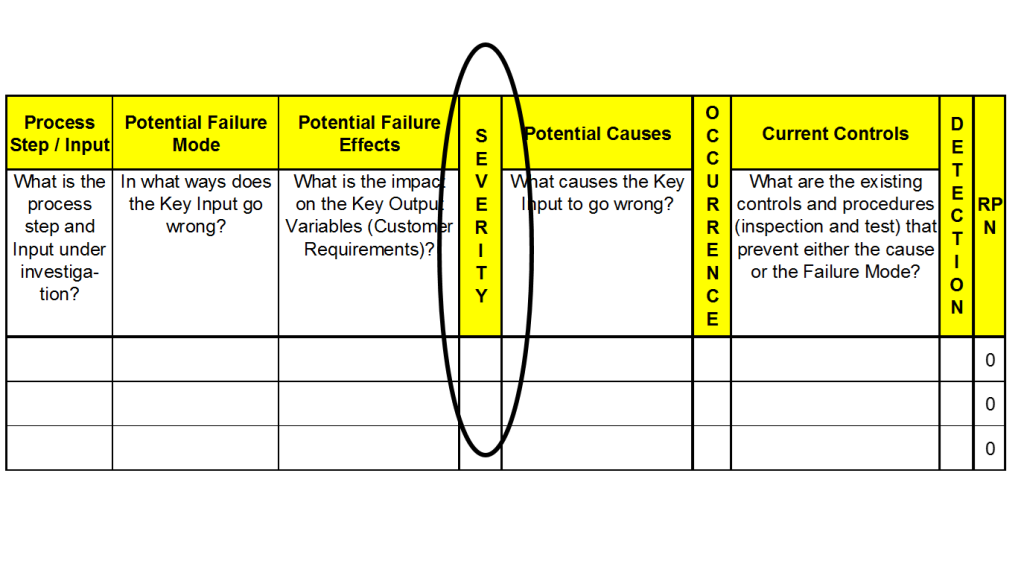
Amostra de uma escala de gravidade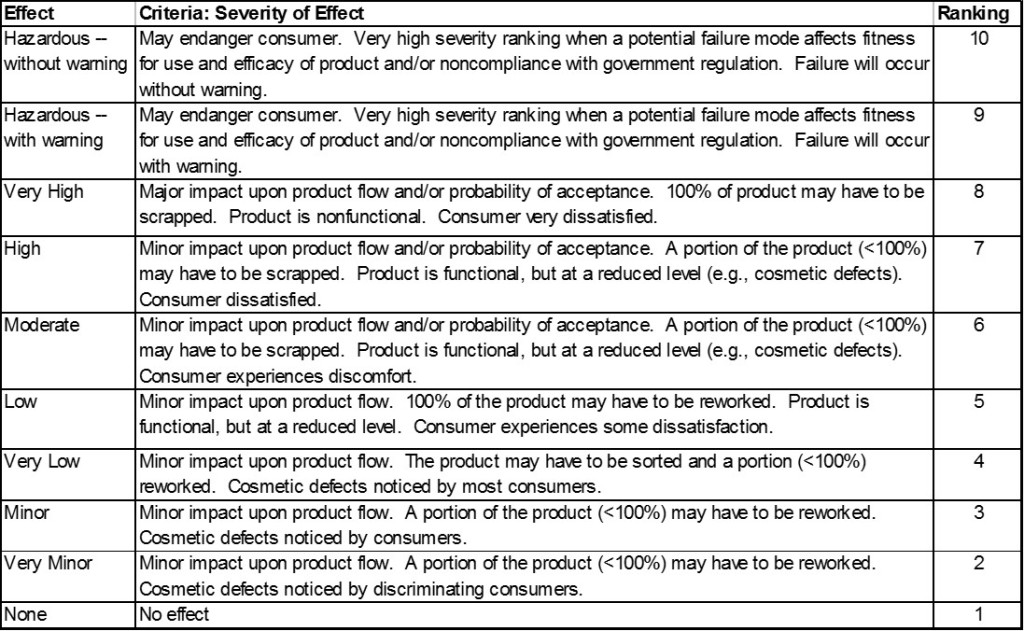
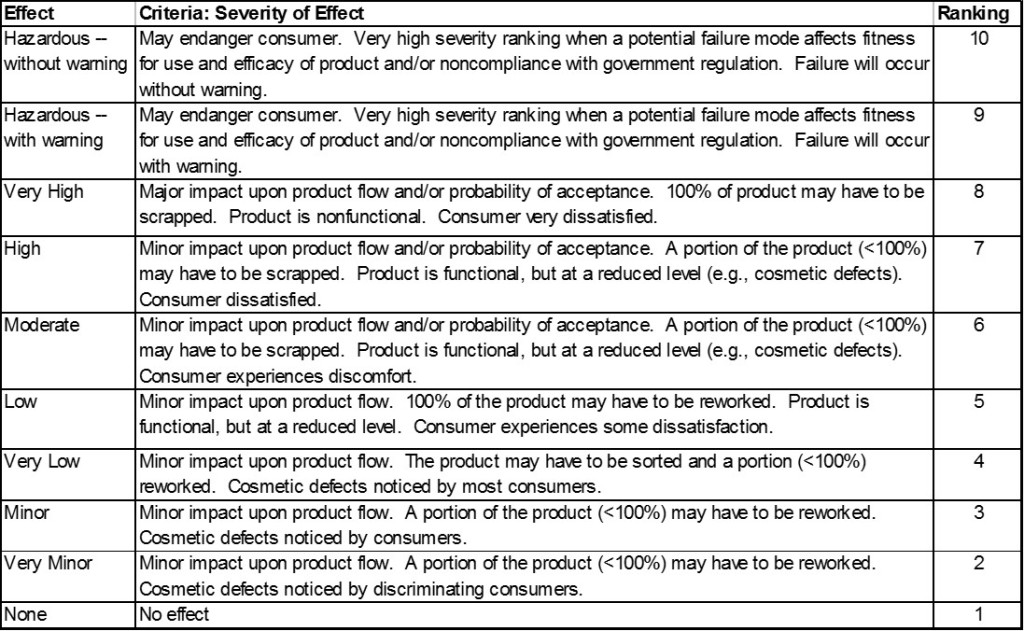
7. Atribuir a Ocorrência Ranking
O Ranking Ocorrência baseia-se na probabilidade, ou frequência, que a causa (ou mecanismo de falha) vai ocorrer.
Uma vez que a causa é conhecida, capturar dados sobre a freqüência de causas. Fontes de dados pode ser sucata e retrabalho relatórios, reclamações de clientes e registros de manutenção de equipamentos. 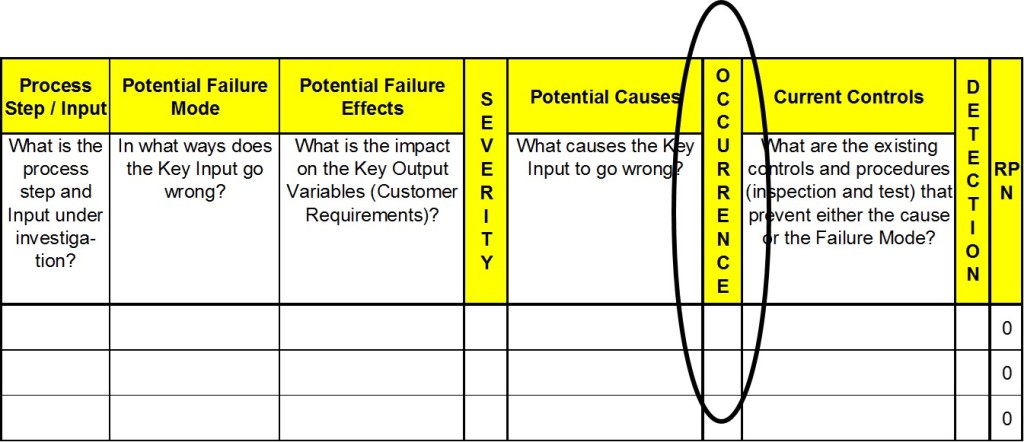
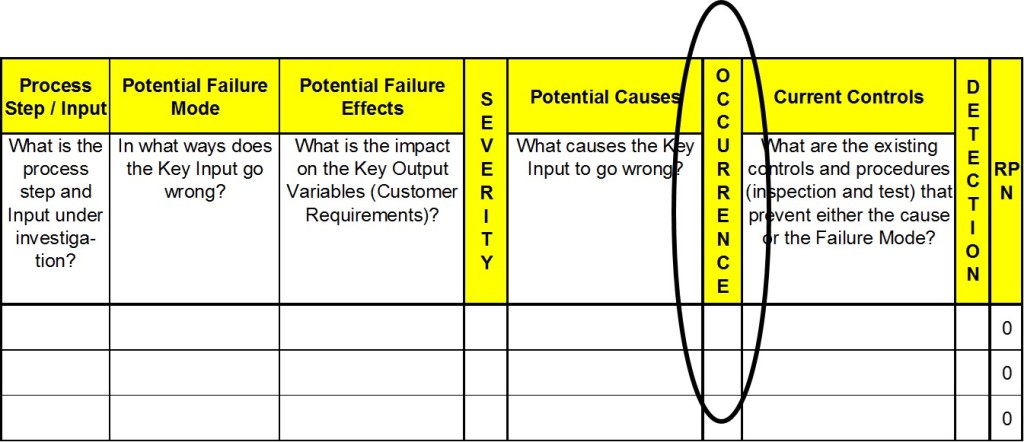
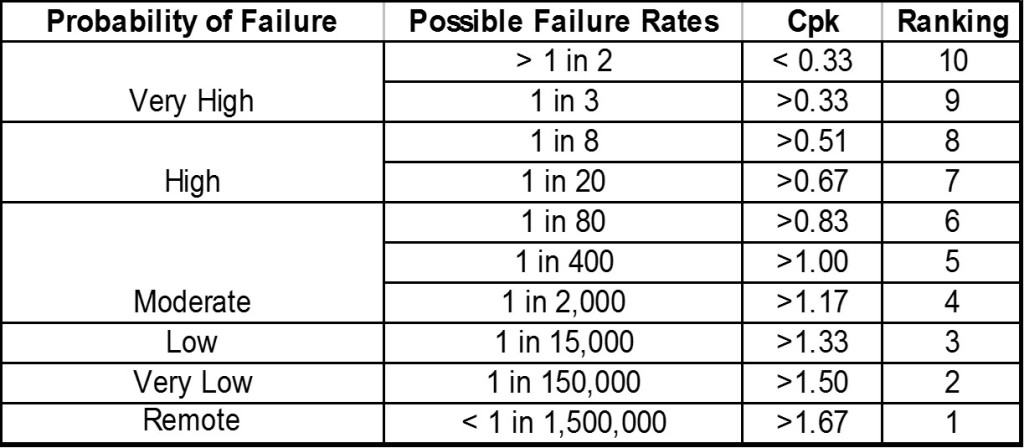
8. Atribuir o classificações Detecção
Para atribuir a classificação de detecção, identificar o processo ou controlos relacionados com o produto no lugar para cada um dos modos de falha e depois atribuir uma classificação de detecção para cada controlo. rankings de detecção de avaliar os controles de processos actualmente em vigor.
Um controlo pode relacionar-se a si mesmo de modo de falha, a causa (ou mecanismo) de falha, ou os efeitos de um modo de falha.
Para tornar os controlos avaliaram ainda mais complexo, os controlos podem impedir um modo de falha ou causa a ocorrência ou detectar um modo de falha, causa da falha, ou efeito de falha após ter ocorrido.

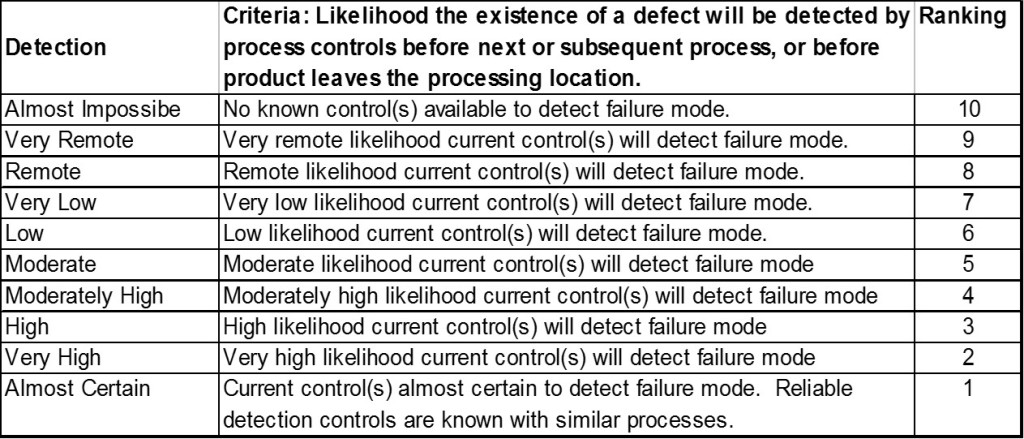
9. Calcular o Número de Prioridade de Risco (RPN)
A RPN é o Número de Prioridade de Risco. A RPN nos dá uma classificação de risco relativo. Quanto maior o RPN, maior o risco potencial.
A RPN é calculado multiplicando-se as três classificações juntos. Multiplique o ranking Times Gravidade da Ocorrência ranking do Times ranking de Detecção.
Calcular a RPN para cada modo de falha e efeito.
Priorizar os riscos, classificando o RPN de maior pontuação para baixo Score. Isto irá ajudar a equipe a determinar os inputs mais críticos e as causas de seu fracasso.
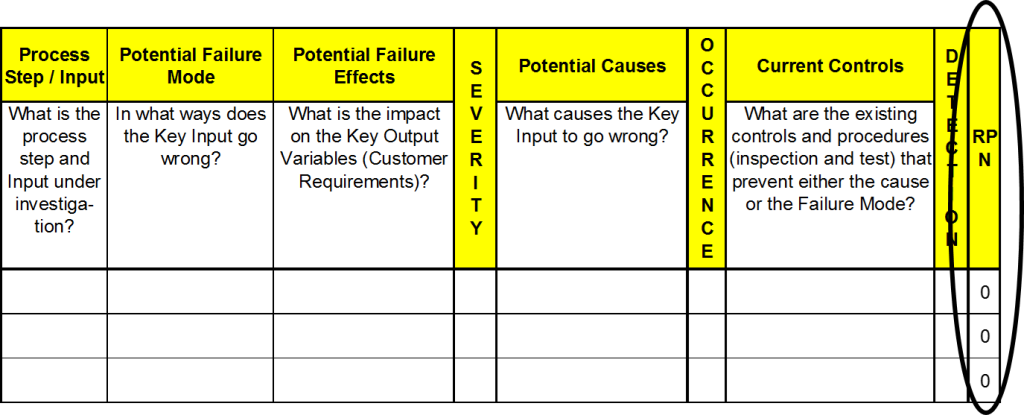
10. Desenvolver Plano de Acção:
Tomando acção significa reduzir a RPN. A RPN pode ser reduzida baixando qualquer das três classificações (gravidade, ocorrência, ou detecção) individualmente ou em combinação um com o outro.
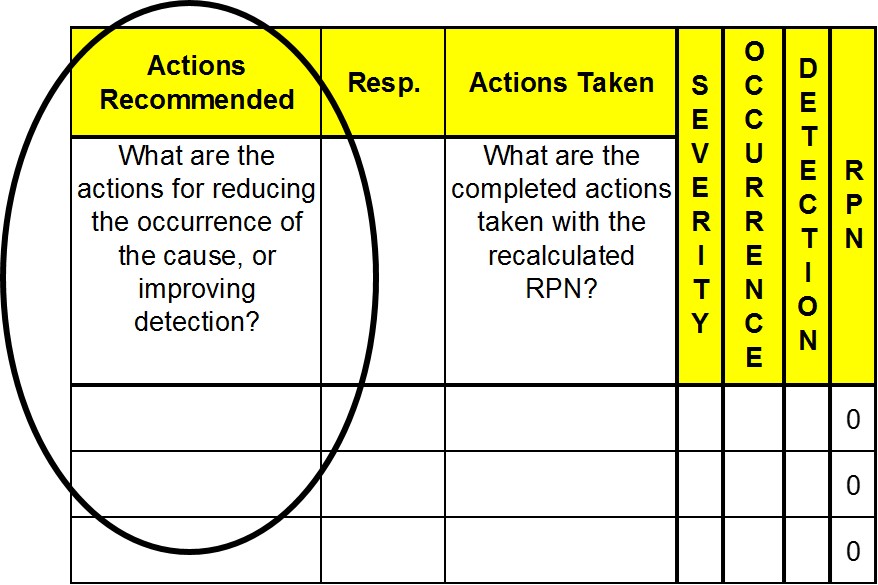
11. Quem é responsável:
Este é um passo muito importante na tomada de medidas!
Certifique-se de incluir pessoa (s) responsável e do prazo
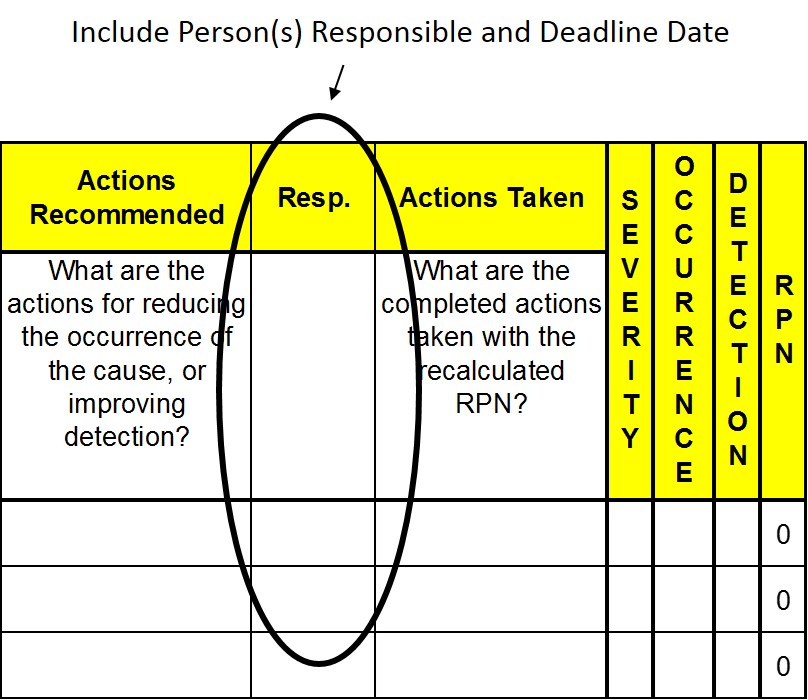
12. agir:
O plano descreve quais os passos necessários para implementar a solução, que vai fazê-las, e quando eles vão ser concluída.
A maioria dos planos de acção identificados durante um PFMEA será do simples “quem, o quê, e quando” categoria.
Responsabilidades e datas de conclusão alvo para ações específicas a serem tomadas são identificados.
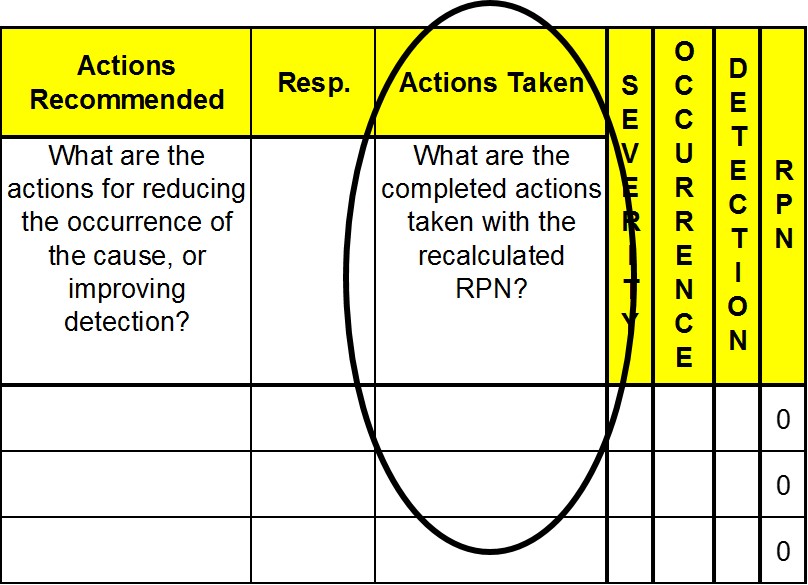
13. recalcular o RPN Resultante:
Este passo de um PFMEA confirma o plano de acção teve os resultados desejados, calculando a RPN resultante. Para recalcular a RPN, reavaliar a gravidade, a ocorrência e rankings de detecção para os modos de falha após o plano de acção foi concluída.